کارخانه های تولید میلگرد تهران شریان های حیاتی صنعت ساخت وساز ایران محسوب می شوند. این کارخانه ها با بهره گیری از دانش مهندسی متالورژی و مکانیک مواد اولیه را به مقاطع فولادی مستحکم تبدیل می کنند که اسکلت ساختمان ها و زیرساخت های مدرن را شکل می دهند. در این مقاله به بررسی جامع این واحد های صنعتی از اصول عملکرد اجزای اصلی تا استانداردهای بین المللی و چالش های پیش رو خواهیم پرداخت.
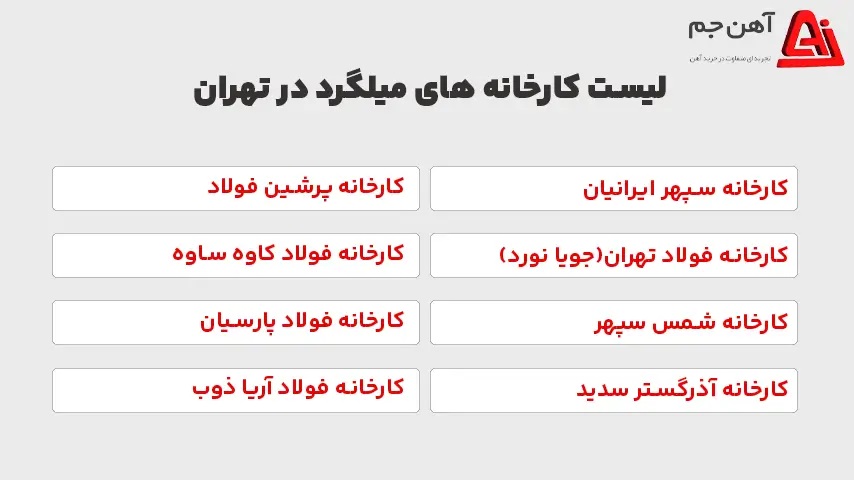
برای مشاهده لیست این کارخانه ها لینک زیر را لمس کنید .
کارخانه های تولید میلگرد تهران
تعریف و عملکرد فنی کارخانه تولید میلگرد
کارخانه تولید میلگرد یک واحد صنعتی پیچیده است که فرآیند تولید میلگردهای فولادی مورد استفاده در صنعت ساخت وساز را انجام می دهد. عملکرد فنی این کارخانه ها بر پایه تغییر شکل پلاستیک فولاد گرم استوار است. به طور خلاصه شمش های فولادی با ابعاد بزرگ وارد کارخانه شده و پس از طی مراحل مختلف حرارتی و مکانیکی به میلگردهای با قطرهای مشخص و خواص مکانیکی معین تبدیل می شوند. هدف اصلی این فرآیند تولید میلگردهایی با مقاومت کششی و شکل پذیری مناسب برای تقویت بتن و تحمل بارهای سازه ای است. این عملکرد حیاتی کارخانه های تولید میلگرد را به رکن اساسی زنجیره تامین صنعت ساخت وساز تبدیل کرده است.
اجزای اصلی و اصول کارکرد کارخانه تولید میلگرد
یک کارخانه تولید میلگرد از بخش های مختلفی تشکیل شده است که هر کدام وظایف خاصی را بر عهده دارند. در ادامه به اجزای اصلی و اصول کارکرد آن ها اشاره می شود :
بیشتر بخوانید: محله محمودیه تهران بهشتی برای زندگی! امتیاز 22
۱. بخش آماده سازی مواد اولیه و کوره سازی
- انبار مواد اولیه : این بخش محل نگهداری مواد اولیه اصلی کارخانه یعنی شمش های فولادی است. شمش ها معمولاً به صورت عمده از کارخانه های فولادسازی بزرگ تهیه می شوند و بر اساس ترکیب شیمیایی و ابعاد مشخص دسته بندی می شوند.
- پیش گرم کن (Preheater) : برخی کارخانه ها از پیش گرم کن برای افزایش دمای اولیه شمش ها قبل از ورود به کوره اصلی استفاده می کنند. این کار به بهبود راندمان حرارتی کوره و کاهش مصرف انرژی کمک می کند. پیش گرم کن ها معمولاً از گازهای خروجی کوره برای گرم کردن شمش ها استفاده می کنند و بر اساس اصل بازیابی حرارت عمل می کنند.
- کوره ذوب و گرمایش (Reheating Furnace) : قلب کارخانه تولید میلگرد کوره گرمایش است. در این بخش شمش های فولادی تا دمای ۱۲۰۰–۱۲۵۰ درجه سانتیگراد گرم می شوند تا برای مرحله نورد آماده شوند. کوره های مورد استفاده معمولاً از نوع کوره های پیوسته (Pusher Type Furnace) یا کوره های گردان (Rotary Hearth Furnace) هستند.
- کوره های پیوسته : در این نوع کوره شمش ها به صورت پیوسته و خطی از میان کوره عبور می کنند و در طول مسیر به تدریج گرم می شوند. حرکت شمش ها توسط مکانیزم های هیدرولیکی یا مکانیکی انجام می شود.
- کوره های گردان : در کوره های گردان کف کوره به صورت دایره ای چرخانده می شود و شمش ها به صورت دورانی در کوره حرکت می کنند. این نوع کوره برای گرمایش یکنواخت تر شمش ها مناسب است.
- سوخت کوره : کوره ها معمولاً با سوخت های فسیلی مانند گاز طبیعی یا مازوت کار می کنند. با این حال تلاش های زیادی برای استفاده از سوخت های جایگزین و افزایش راندمان انرژی کوره ها در حال انجام است. اصول انتقال حرارت (هدایت همرفت و تابش) در طراحی و عملکرد کوره ها نقش اساسی دارند.
۲. بخش نورد
- قفسه های نورد (Rolling Stands) : بخش نورد اصلی ترین قسمت کارخانه تولید میلگرد است. در این بخش شمش های گرم شده از میان مجموعه ای از قفسه های نورد عبور می کنند و به تدریج تغییر شکل داده و به قطر و شکل نهایی میلگرد تبدیل می شوند. قفسه های نورد شامل غلتک هایی هستند که با حرکت دورانی و فشار سطح مقطع شمش را کاهش می دهند.
- انواع قفسه های نورد : قفسه های نورد بر اساس نوع آرایش غلتک ها و جهت نورد به انواع مختلفی تقسیم می شوند از جمله :
- قفسه های نورد اولیه (Roughing Stands) : این قفسه ها در ابتدای خط نورد قرار دارند و وظیفه آن ها کاهش اولیه سطح مقطع شمش و تبدیل آن به بلوم یا بیلت است.
- قفسه های نورد میانی (Intermediate Stands) : قفسه های میانی ابعاد بلوم یا بیلت را بیشتر کاهش داده و شکل اولیه میلگرد را ایجاد می کنند.
- قفسه های نورد نهایی (Finishing Stands) : قفسه های نهایی شکل و ابعاد نهایی میلگرد را تعیین می کنند و سطح آن را صاف و یکنواخت می کنند.
- غلتک های نورد (Rolling Rolls) : غلتک ها ابزارهای اصلی تغییر شکل فولاد در فرآیند نورد هستند. جنس غلتک ها معمولاً از فولادهای آلیاژی سخت و مقاوم به سایش انتخاب می شود. طراحی پروفیل غلتک ها به گونه ای است که شکل نهایی میلگرد را ایجاد کند. نیروهای نورد و اصطکاک بین غلتک ها و فولاد از عوامل مهم در فرآیند نورد هستند.
بیشتر بخوانید: مدارک لازم برای سفارت سوئد در تهران
۳. بخش خنک کاری و عملیات حرارتی
- بستر خنک کن (Cooling Bed) : میلگردهای گرم پس از خروج از قفسه های نورد نهایی وارد بستر خنک کن می شوند. هدف از خنک کاری کاهش دمای میلگردها و ایجاد ساختار متالورژیکی مناسب است. خنک کاری می تواند به صورت طبیعی (هوا خنک) یا اجباری (آب خنک) انجام شود.
- خنک کاری کنترل شده (Controlled Cooling) : در برخی کارخانه ها از سیستم های خنک کاری کنترل شده استفاده می شود تا سرعت خنک کاری میلگردها را به دقت تنظیم کنند. این کار به بهبود خواص مکانیکی میلگردها به ویژه مقاومت تسلیم و شکل پذیری کمک می کند. فرآیند خنک کاری کنترل شده بر اساس اصول دگرگونی فازی فولاد و سینتیک آن انجام می شود.
- عملیات حرارتی (Heat Treatment) : در برخی موارد میلگردها پس از نورد و خنک کاری تحت عملیات حرارتی قرار می گیرند تا خواص مکانیکی آن ها بهبود یابد. عملیات حرارتی می تواند شامل تمپر کردن (Tempering) آنیل کردن (Annealing) یا نرمالیزه کردن (Normalizing) باشد. نوع عملیات حرارتی به نوع فولاد و خواص مکانیکی مورد نظر بستگی دارد.
۴. بخش برش و بسته بندی
- دستگاه برش (Shearing Machine) : میلگردهای خنک شده و عملیات حرارتی شده به طول های استاندارد برش داده می شوند. دستگاه های برش معمولاً از نوع برش گیوتینی یا برش دیسکی هستند. دقت برش و کیفیت سطح برش از اهمیت بالایی برخوردار است.
- بسته بندی (Bundling) : میلگردهای برش داده شده دسته بندی و بسته بندی می شوند. بسته بندی معمولاً به صورت بندیل های وزنی انجام می شود و وزن هر بندیل بر اساس سفارش مشتری و استانداردهای مربوطه تعیین می شود. بسته بندی مناسب از زنگ زدگی و آسیب دیدن میلگردها در حین حمل و نقل و انبارداری جلوگیری می کند.
- علامت گذاری (Marking) : بندیل های میلگرد با اطلاعات مربوط به کارخانه تولیدکننده نوع فولاد قطر میلگرد شماره ذوب و استانداردهای مربوطه علامت گذاری می شوند. علامت گذاری دقیق و خوانا قابلیت ردیابی (Traceability) محصول را تضمین می کند.
بیشتر بخوانید: تعمیرکار شوفاژ شرق تهران
۵. بخش کنترل کیفیت و آزمایشگاه
- آزمایشگاه متالورژی و مکانیک : کنترل کیفیت در تمام مراحل تولید میلگرد از مواد اولیه تا محصول نهایی از اهمیت بسیار بالایی برخوردار است. آزمایشگاه کارخانه وظیفه انجام آزمایش های مختلف بر روی نمونه های میلگرد را بر عهده دارد. این آزمایش ها شامل :
- آزمایش کشش (Tensile Test) : برای تعیین مقاومت کششی مقاومت تسلیم و درصد ازدیاد طول میلگرد.
- آزمایش خمش (Bending Test) : برای بررسی شکل پذیری و مقاومت به ترک خوردگی میلگرد.
- آزمایش سختی (Hardness Test) : برای تعیین سختی میلگرد.
- آنالیز شیمیایی (Chemical Analysis) : برای تعیین ترکیب شیمیایی فولاد و مطابقت آن با استانداردهای مربوطه.
- بازرسی ابعادی (Dimensional Inspection) : برای بررسی قطر پروفیل و طول میلگرد و مطابقت آن با تلرانس های مجاز.
- سیستم های کنترل فرآیند (Process Control Systems) : کارخانه های مدرن تولید میلگرد از سیستم های کنترل فرآیند پیشرفته برای مانیتورینگ و کنترل دقیق پارامترهای مختلف تولید استفاده می کنند. این سیستم ها با جمع آوری داده ها از حسگرهای مختلف در خط تولید امکان بهینه سازی فرآیند و بهبود کیفیت محصول را فراهم می کنند. اتوماسیون صنعتی و هوش مصنوعی نقش فزاینده ای در این سیستم ها ایفا می کنند.
کاربردهای صنعتی و مثال هایی از صنایع مختلف
میلگرد فولادی یکی از پرکاربردترین مصالح ساختمانی در جهان است و در صنایع مختلفی کاربرد دارد. مهم ترین کاربردهای صنعتی میلگرد عبارتند از :
- صنعت ساختمان : اصلی ترین کاربرد میلگرد تقویت بتن مسلح در ساختمان های مسکونی تجاری و صنعتی است. میلگردها در ستون ها تیرها سقف ها دیوارها و فونداسیون ها استفاده می شوند تا مقاومت کششی بتن را افزایش داده و سازه را در برابر بارهای مختلف مقاوم کنند.
- صنعت زیرساخت : میلگرد در پروژه های زیرساختی بزرگ مانند پل ها تونل ها راه ها سدها و نیروگاه ها به وفور استفاده می شود. این سازه ها به میلگردهای با کیفیت بالا و خواص مکانیکی ویژه نیاز دارند تا در شرایط محیطی سخت و بارهای سنگین عملکرد ایمن و پایداری داشته باشند.
- صنعت راه آهن : میلگرد در ساخت ریل های راه آهن و تراورس ها استفاده می شود. ریل های راه آهن باید مقاومت بالایی در برابر بارهای دینامیکی و خستگی داشته باشند.
- صنعت خودروسازی : میلگرد در ساخت برخی قطعات خودرو مانند شاسی و بدنه استفاده می شود. در این صنعت میلگردهای با استحکام بالا و وزن کم مورد توجه هستند.
- صنعت نفت و گاز : میلگرد در ساخت سازه های فلزی سکوی های نفتی و خطوط لوله استفاده می شود. این سازه ها باید در برابر شرایط محیطی خورنده و بارهای سنگین مقاوم باشند.
مثال هایی از صنایع مختلف :
- ساختمان برج میلاد تهران : در ساخت این برج بلندمرتبه از هزاران تن میلگرد با قطرهای مختلف و گریدهای گوناگون استفاده شده است.
- پروژه پل صدر تهران : در ساخت این پل بزرگ میلگرد نقش کلیدی در تقویت بتن عرشه پل و پایه های آن ایفا کرده است.
- خطوط متروی تهران : میلگرد در ساخت تونل ها و ایستگاه های مترو برای تقویت بتن و افزایش پایداری سازه استفاده شده است.
بررسی استانداردهای بین المللی و فناوری های پیشرفته مرتبط
صنعت تولید میلگرد تحت تاثیر استانداردهای بین المللی و فناوری های پیشرفته قرار دارد. رعایت این استانداردها و بهره گیری از فناوری های نوین نقش مهمی در بهبود کیفیت محصول افزایش راندمان تولید و کاهش هزینه ها ایفا می کند.
استانداردهای بین المللی :
- استاندارد ASTM (انجمن مواد و آزمون آمریکا) : استانداردهای ASTM از جمله معتبرترین استانداردهای جهانی در زمینه مواد و مصالح ساختمانی هستند. استاندارد ASTM A۶۱۵ و ASTM A۷۰۶ به طور خاص به مشخصات میلگردهای فولادی برای بتن مسلح می پردازند و ویژگی های مکانیکی شیمیایی و ابعادی میلگردها را تعیین می کنند.
- استاندارد ISO (سازمان بین المللی استانداردسازی) : استانداردهای ISO نیز در سطح جهانی مورد استفاده قرار می گیرند. استاندارد ISO ۶۹۳۵ به مشخصات میلگردهای فولادی جوش پذیر برای بتن مسلح می پردازد.
- استاندارد EN (استاندارد اروپایی) : استانداردهای EN در کشورهای اروپایی و بسیاری از کشورهای دیگر به عنوان مبنای تولید و مصرف میلگرد مورد استفاده قرار می گیرند. استاندارد EN ۱۰۰۸۰ به مشخصات میلگردهای فولادی جوش پذیر برای بتن مسلح می پردازد.
- استاندارد ملی ایران (ISIRI) : سازمان ملی استاندارد ایران نیز استانداردهای ملی برای تولید میلگرد تدوین کرده است. استاندارد ISIRI ۳۱۳۲ به مشخصات میلگردهای فولادی گرم نوردیده برای بتن مسلح می پردازد و بر اساس استانداردهای بین المللی تدوین شده است.
فناوری های پیشرفته مرتبط :
- اتوماسیون و رباتیک : استفاده از سیستم های اتوماسیون و رباتیک در خطوط تولید میلگرد به افزایش سرعت تولید کاهش خطای انسانی و بهبود کیفیت محصول کمک می کند. ربات ها می توانند در بخش های مختلفی از جمله بارگیری و تخلیه شمش ها کنترل فرآیند نورد بسته بندی و انبارداری به کار گرفته شوند.
- سیستم های کنترل کیفیت آنلاین : سیستم های کنترل کیفیت آنلاین با استفاده از حسگرهای پیشرفته و پردازش داده های لحظه ای امکان پایش مستمر کیفیت محصول در طول فرآیند تولید را فراهم می کنند. این سیستم ها می توانند عیوب احتمالی را به سرعت شناسایی کرده و از تولید محصولات نامنطبق جلوگیری کنند.
- فناوری های نوین کوره سازی : توسعه کوره های با راندمان حرارتی بالا و مصرف انرژی پایین از جمله اولویت های صنعت فولاد است. استفاده از فناوری های نوین مانند کوره های القایی کوره های قوس الکتریکی DC و سیستم های بازیابی حرارت به کاهش هزینه های تولید و اثرات زیست محیطی کمک می کند.
- نورد گرم کنترل شده (Thermo-Mechanical Control Processing – TMCP) : فناوری TMCP ترکیبی از نورد گرم و خنک کاری کنترل شده است که به تولید میلگردهایی با خواص مکانیکی بهبود یافته و مصرف آلیاژ کمتر منجر می شود. این فناوری بر اساس کنترل دقیق دما و سرعت نورد و خنک کاری ساختار متالورژیکی ریزدانه و یکنواختی را در میلگرد ایجاد می کند.
- تولید میلگردهای با استحکام بالا (High-Strength Rebar) : با پیشرفت فناوری و نیاز به سازه های بلندتر و سبک تر تقاضا برای میلگردهای با استحکام بالا افزایش یافته است. تولید میلگردهای با استحکام بالا نیازمند استفاده از فولادهای آلیاژی خاص و فرآیندهای تولید پیشرفته است.
چالش ها و محدودیت های فنی
صنعت تولید میلگرد با چالش ها و محدودیت های فنی متعددی روبرو است که نیازمند توجه و راهکارهای نوآورانه هستند :
- مصرف انرژی بالا : فرآیند تولید میلگرد به ویژه در بخش کوره سازی و نورد انرژی بسیار زیادی مصرف می کند. افزایش قیمت انرژی و نگرانی های زیست محیطی ضرورت کاهش مصرف انرژی و افزایش راندمان انرژی را دوچندان کرده است.
- آلایندگی محیط زیست : کوره های فولادسازی و فرآیندهای نورد می توانند آلاینده های مختلفی از جمله گازهای گلخانه ای ذرات معلق و پساب های صنعتی تولید کنند. رعایت استانداردهای زیست محیطی و استفاده از فناوری های کاهش آلودگی از الزامات اساسی کارخانه های تولید میلگرد است.
- رقابت شدید : بازار میلگرد بازاری رقابتی است و کارخانه ها برای حفظ سهم بازار و سودآوری باید به طور مداوم به دنبال بهبود کیفیت محصول کاهش هزینه ها و افزایش بهره وری باشند.
- نوسانات قیمت مواد اولیه : قیمت مواد اولیه اصلی تولید میلگرد یعنی شمش فولادی و آهن قراضه تحت تاثیر عوامل مختلف اقتصادی و سیاسی نوسانات زیادی دارد. مدیریت ریسک نوسانات قیمت مواد اولیه از چالش های مهم کارخانه های تولید میلگرد است.
- نیاز به نیروی انسانی متخصص : صنعت تولید میلگرد صنعتی پیچیده و تخصصی است و نیازمند نیروی انسانی ماهر و متخصص در زمینه های مختلف مهندسی متالورژی مکانیک برق و اتوماسیون است. جذب و نگهداشت نیروی انسانی متخصص از چالش های مهم این صنعت است.
- فرسودگی تجهیزات : برخی از کارخانه های تولید میلگرد در ایران از تجهیزات قدیمی و فرسوده استفاده می کنند که راندمان تولید را کاهش داده و هزینه های نگهداری و تعمیرات را افزایش می دهد. نوسازی و به روزرسانی تجهیزات از اولویت های سرمایه گذاری در این صنعت است.
نکات کلیدی برای بهینه سازی و بهبود عملکرد
برای بهینه سازی و بهبود عملکرد کارخانه های تولید میلگرد می توان به نکات کلیدی زیر توجه کرد :
- بهینه سازی مصرف انرژی : اجرای اقدامات بهینه سازی انرژی در تمام بخش های کارخانه از جمله کوره سازی نورد خنک کاری و سیستم های روشنایی و تهویه مطبوع می تواند به کاهش هزینه ها و اثرات زیست محیطی کمک کند. استفاده از کوره های با راندمان بالا سیستم های بازیابی حرارت و بهینه سازی فرآیند نورد از جمله این اقدامات هستند.
- ارتقای کیفیت محصول : تمرکز بر کنترل کیفیت در تمام مراحل تولید از مواد اولیه تا محصول نهایی می تواند به بهبود کیفیت میلگردها و افزایش رضایت مشتریان منجر شود. استفاده از سیستم های کنترل کیفیت آنلاین آزمایشگاه های مجهز و آموزش پرسنل در زمینه کنترل کیفیت از جمله اقدامات موثر هستند.
- افزایش بهره وری تولید : بهینه سازی فرآیندهای تولید اتوماسیون خطوط تولید و بهبود مدیریت زنجیره تامین می تواند به افزایش بهره وری تولید و کاهش هزینه های تولید کمک کند.
- کاهش آلایندگی محیط زیست : اجرای اقدامات کاهش آلودگی و رعایت استانداردهای زیست محیطی از جمله مسئولیت های اجتماعی کارخانه های تولید میلگرد است. استفاده از فیلترهای غبارگیر سیستم های تصفیه پساب و فناوری های کاهش انتشار گازهای گلخانه ای از جمله این اقدامات هستند.
- سرمایه گذاری در تحقیق و توسعه : سرمایه گذاری در تحقیق و توسعه (R&D) برای توسعه فناوری های نوین تولید میلگرد بهبود خواص محصول و کاهش هزینه ها می تواند به افزایش رقابت پذیری کارخانه ها در بلندمدت کمک کند.
- آموزش و توانمندسازی نیروی انسانی : ارتقای دانش و مهارت نیروی انسانی از طریق برنامه های آموزشی مستمر و به روزرسانی دانش فنی می تواند به بهبود عملکرد کارخانه و افزایش بهره وری نیروی کار منجر شود.
نتیجه گیری علمی و تخصصی
صنعت تولید میلگرد تهران نقش حیاتی در توسعه زیرساخت های کشور ایفا می کند. این صنعت با بهره گیری از اصول مهندسی متالورژی و مکانیک شمش های فولادی را به میلگردهای مستحکم و با کیفیت تبدیل می کند که اسکلت سازه های مدرن را شکل می دهند. با توجه به چالش ها و محدودیت های فنی پیش رو بهینه سازی مصرف انرژی ارتقای کیفیت محصول افزایش بهره وری تولید و کاهش آلایندگی محیط زیست از اولویت های اساسی این صنعت محسوب می شوند. رعایت استانداردهای بین المللی بهره گیری از فناوری های پیشرفته و سرمایه گذاری در تحقیق و توسعه کلید موفقیت و پایداری کارخانه های تولید میلگرد در آینده خواهد بود. همچنین توجه به آموزش و توانمندسازی نیروی انسانی متخصص نقش مهمی در ارتقای سطح کیفی و فنی این صنعت ایفا خواهد کرد.
پرسش و پاسخ
۱. چه عواملی بر کیفیت میلگرد تولیدی یک کارخانه تاثیر می گذارند؟
کیفیت میلگرد به عوامل متعددی بستگی دارد که مهم ترین آن ها عبارتند از :
- کیفیت مواد اولیه (شمش فولادی) : ترکیب شیمیایی ساختار متالورژیکی و کیفیت سطح شمش فولادی تاثیر مستقیمی بر کیفیت میلگرد نهایی دارد. استفاده از شمش های با کیفیت و مطابق با استانداردهای مربوطه از الزامات تولید میلگرد با کیفیت است.
- فرآیند تولید : کنترل دقیق دما سرعت نورد خنک کاری و عملیات حرارتی در طول فرآیند تولید نقش تعیین کننده ای در خواص مکانیکی و ساختار متالورژیکی میلگرد دارد. بهینه سازی پارامترهای فرآیند تولید و استفاده از فناوری های پیشرفته به بهبود کیفیت محصول کمک می کند.
- کنترل کیفیت : انجام آزمایش های کنترل کیفیت در مراحل مختلف تولید از مواد اولیه تا محصول نهایی و اطمینان از مطابقت محصول با استانداردهای مربوطه از عوامل کلیدی در تضمین کیفیت میلگرد است.
۲. چه استانداردهایی برای میلگرد در ایران و جهان وجود دارد؟
در ایران استاندارد ملی ایران ISIRI ۳۱۳۲ اصلی ترین استاندارد برای میلگردهای فولادی گرم نوردیده برای بتن مسلح است. این استاندارد بر اساس استانداردهای بین المللی تدوین شده است و مشخصات فنی و روش های آزمون میلگردها را تعیین می کند. در سطح بین المللی استانداردهای ASTM A۶۱۵ ASTM A۷۰۶ ISO ۶۹۳۵ و EN ۱۰۰۸۰ از جمله استانداردهای معتبر و پرکاربرد برای میلگرد هستند که در کشورهای مختلف مورد استفاده قرار می گیرند. این استانداردها ویژگی های مکانیکی شیمیایی ابعادی و روش های آزمون میلگردها را مشخص می کنند و به تضمین کیفیت و ایمنی سازه های بتن مسلح کمک می کنند.
۳. چگونه می توان مصرف انرژی در کارخانه های تولید میلگرد را کاهش داد؟
کاهش مصرف انرژی در کارخانه های تولید میلگرد از طریق اقدامات مختلفی امکان پذیر است از جمله :
- بهینه سازی کوره ها : استفاده از کوره های با راندمان حرارتی بالا عایق کاری مناسب کوره ها کنترل دقیق احتراق و استفاده از سیستم های پیش گرم کن و بازیابی حرارت می تواند به کاهش مصرف سوخت و انرژی در بخش کوره سازی کمک کند.
- بهینه سازی فرآیند نورد : کاهش تعداد پاس های نورد استفاده از غلتک های با طراحی بهینه کنترل دقیق دما و سرعت نورد و کاهش اصطکاک می تواند به کاهش انرژی مورد نیاز برای فرآیند نورد منجر شود.
- استفاده از سیستم های خنک کاری کارآمد : بهینه سازی سیستم های خنک کاری میلگردها و استفاده از سیستم های بازیابی حرارت از آب خنک کن می تواند به کاهش مصرف انرژی در بخش خنک کاری کمک کند.
- بهبود سیستم های روشنایی و تهویه مطبوع : استفاده از لامپ های LED کم مصرف سیستم های تهویه مطبوع با راندمان بالا و عایق کاری ساختمان های کارخانه می تواند به کاهش مصرف انرژی در بخش های غیرتولیدی کارخانه کمک کند.
- مدیریت مصرف انرژی : استقرار سیستم های مدیریت انرژی پایش مستمر مصرف انرژی و شناسایی و رفع نقاط پرت انرژی می تواند به کاهش کلی مصرف انرژی در کارخانه منجر شود.